What Is Oil Canning? Definition, Causes, & How to Minimize it
Oil canning is a visual phenomenon that can occur with standing seam metal roof and wall panel systems. Discover why oil canning occurs, what to look for during installation, and...
What Is Oil Canning?
Oil canning is defined as the perceived waviness of a metal panel and is an inherent characteristic of light-gauge, cold-rolled flat metal products. In other words, it’s a visual phenomenon that makes metal panels look wavy or somewhat distorted, especially in the broad, flat areas of a metal roof or wall system. Oil canning can occur with any type of metal material used in construction, including:
- Steel
- Galvalume®
- Galvanized
- Stainless
- Copper
- Zinc
- Aluminum
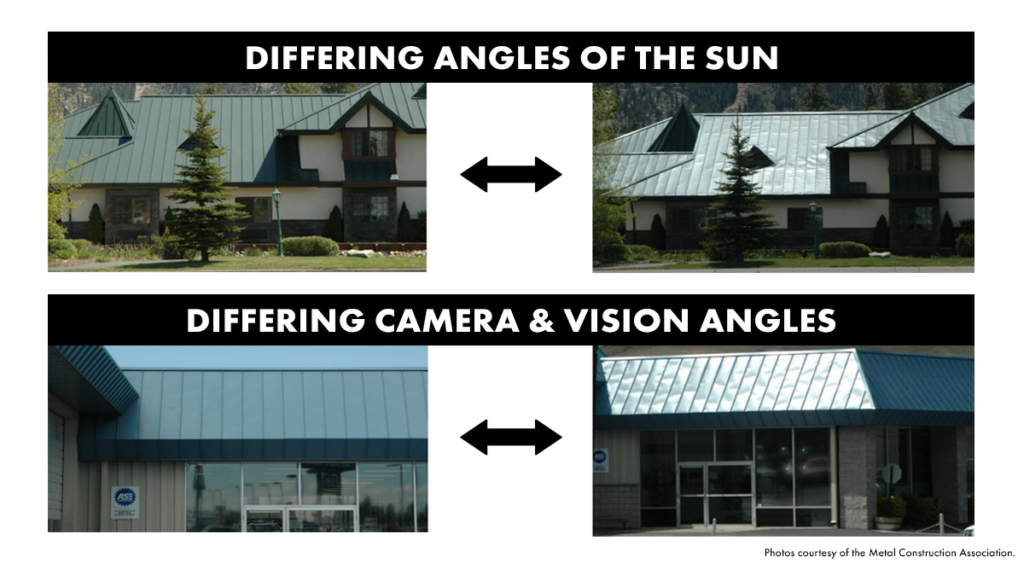
The severity of the waviness varies quite a bit depending on the color, finish, time of day, time of year, or even just the angle the metal is viewed from, which is why no real concrete method or scale for measuring it exists.
A silver lining of oil canning is that, if it does occur, it’s just a cosmetic surface-level issue and doesn’t affect the structural integrity of the panel system. This is why nearly all warranties, whether it be weathertight, substrate, or paint warranties, don’t include oil canning as a viable claim because there technically isn’t anything that would cause the roof to fail for that reason alone.
Luckily, there are known causes and ways to minimize the chance for oil canning, which we will define and discuss next.

Causes of Oil Canning on Metal Roofing & Wall Systems
We will be truthful with you, there are many different causes factoring into the development of oil canning, and it can be hard to pin down the root cause in some cases. Here is a comprehensive listing of the most prominent reasons oil canning occurs.
Stresses during the production process
Oil canning can sometimes occur during the early stages of the flattening and coiling production. According to the Metal Construction Association (MCA), there are three separate stresses that can be inflicted on the metal during production that could lead to the development of oil canning:
- Full center – When the sheet or coil is longer in the middle section, which creates ripples or buckles along the center.
- Wavy edge – When the edge of the sheet or coil is longer along the edge of the strip.
- Camber – When the coil or sheet deviates from a straight line when laid flat (think of the curvature of a banana).
Stresses during rollforming and slitting
All metals have a memory and the material is always trying to revert back to its original form. This is why the stresses inflicted during rollforming and slitting of the metal coil and sheets can facilitate oil canning as the metal moves and warps when attempting to go back to its previous form.
Color and gloss type
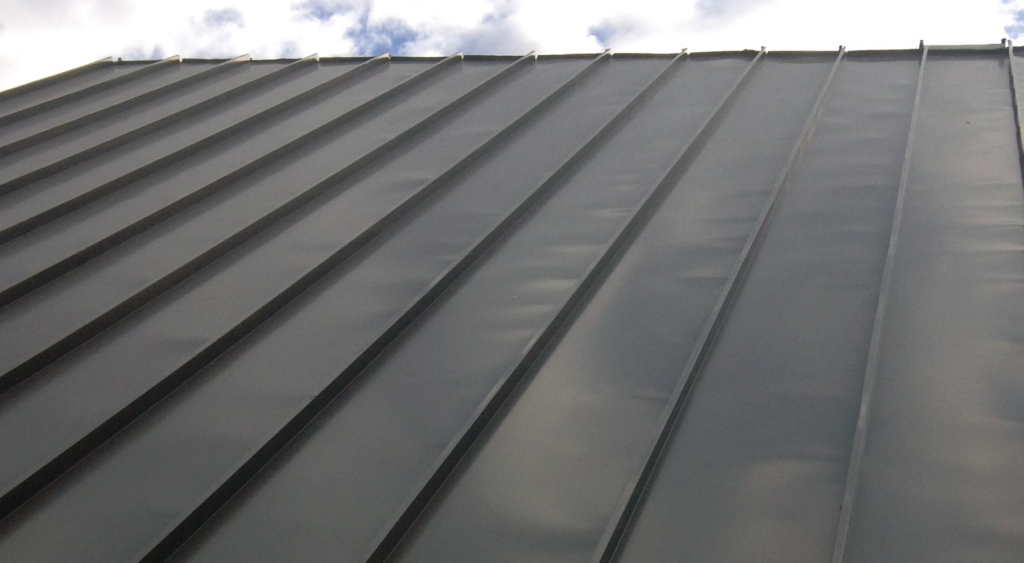
Any color or gloss type has the same chance of developing oil canning, but darker colors and high-gloss finishes tend to show the effects/waviness more than lighter colors and low-gloss finishes.
Incorrect fastener installation
There are two common situations where fasteners could be attributed to the development of oil canning:
- Over-driving fasteners: The over-driving of fasteners can cause stress to the male leg of the panel. This is especially present with standing seam metal roofing systems where the panels are connected directly to the support system.
- Angling fasteners: Like over-driving, driving in the fastener at an angle when attaching the panel to the roof deck can create unnecessary stress that could lead to oil canning.
Improper usage, handling, and storage by installers
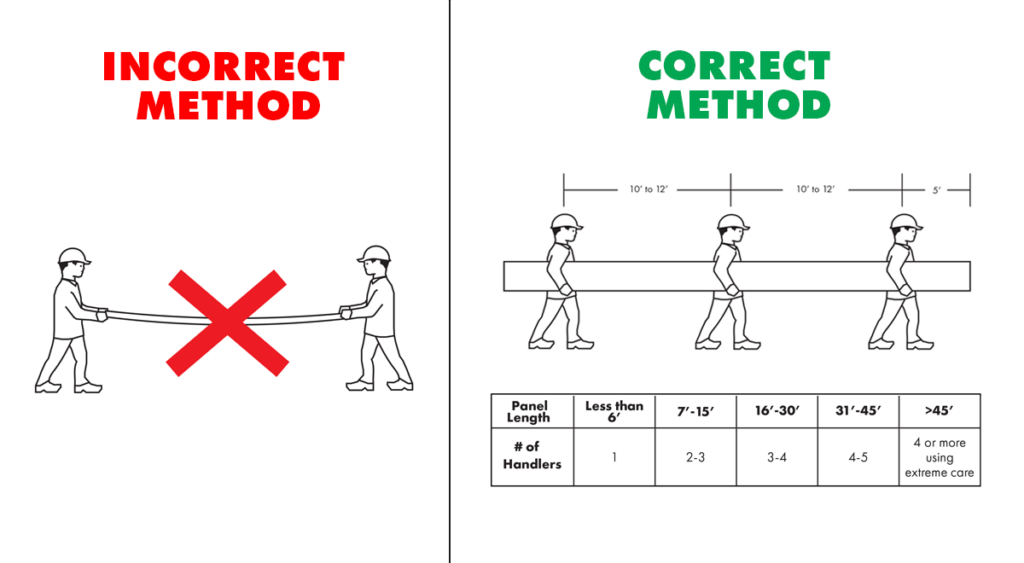
Metal coils and sheets, both before and after rollforming or slitting, require specific care and support. Installers should always carry the panels perpendicular to the ground and ensure they are supported every 10 to 12 feet (as the photo shows). Additionally, other constant moving, twisting, and handling of panels can allow for more opportunities to damage the panel. As always, the manufacturer’s recommendations for handling should always be followed to minimize the chance of oil canning.
Misalignment of the panels
This is a situation where precise measurement and installation is key. For example, if the panels from ridge to eave are misaligned, stresses put on the metal to compensate for and correct the misalignment without redoing the paneling could lead to oil canning.
Inadequate space allotted for thermal movement
When you restrict the expansion and contraction needed for proper thermal movement of a metal panel, you can run into an oil canning issue, as well as other potential problems. This is a common occurrence when panels are double pinned at the edges, which restricts the centers from moving during thermal expansion/contraction and causes stress on the metal.
Structural changes that put tension on the panels
This occurs when the home or building that a metal roof or wall system is installed on changes, moves, or experiences something that makes it different from its original form. Oil canning can happen if there is enough of a change that it puts tension or stress on the metal panels. This is a little more infrequent of an occurrence but is possible if subjected to extreme weathering that affects building structures.
Other stresses to the panel
Some other oil canning causes include:
- Not installing to the correct dimensions of the wall or metal roofing system
- Out of tolerance roof deck, such as concave, convex, or uneven planes
- Clips are too tight against the male leg of the panel
- Clips are too loose against the male leg
There are many different factors that can allow for oil canning to occur. The most important thing to keep in mind is that causing any unnecessary stress, movement, or tension on the metal panels opens the door for oil canning to develop.
What to Look for Before & During Installation
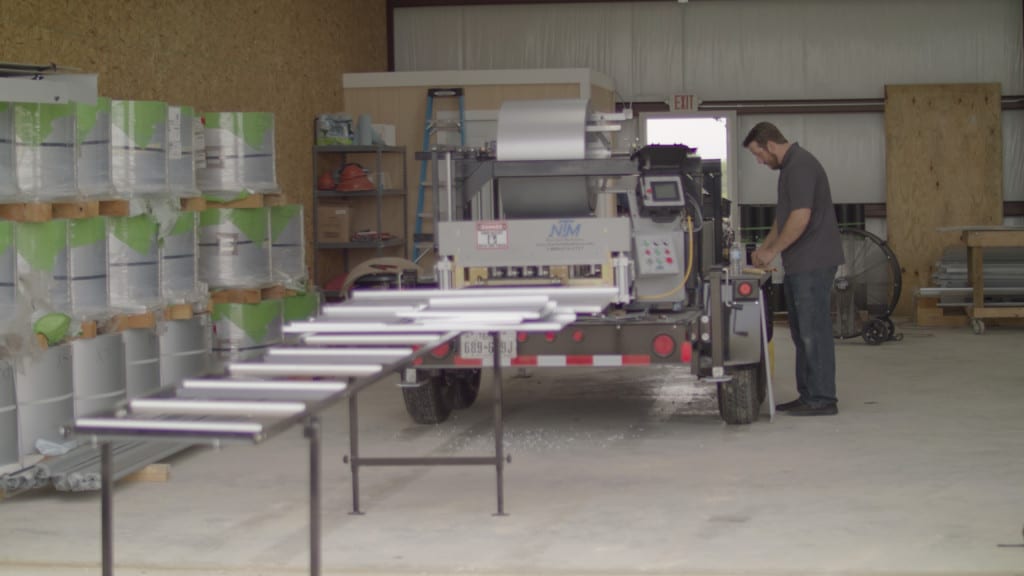
Before we get into the specific ways to minimize the possibility for oil canning to occur, let’s run through a checklist of metal roofing parts for contractors, installers, and home or building owners to observe before and during installation:
- Storage – Locate the storage area and confirm the condition of packaged or crated materials is dry, protected, supported, and positioned so as to not allow any unusual twisting or stress on the materials.
- Panels – Remove one or two panels from a bundle and hang them horizontally from their side and support them along the top rib every 10 to 12 feet, using aligned supports or available workers to confirm flatness or signs of oil canning. Additionally, take note of how the panels are handled when fed through rollforming equipment and/or slitters.
- Panel handling – Request that the panels be moved in a normal manner, and observe them being moved in both horizontal and vertical orientation, to the site where they are to be installed. While doing this, observe the panels to confirm flatness or signs of oil canning.
- Roof decking – Lay the panels onto the same material that they are to be installed upon. Leave them flat and loose, no attachments whatsoever, and observe the panels to confirm flatness or signs of oil canning. Additionally, check the roof deck for any bowing, both concave and convex, or uneven planes that could affect the metal panels.
- Initial installation – Install a panel to an already adjoining panel and observe for flatness or signs of oil canning.
- Installation – Install clips and fasteners as per the manufacturer’s instructions by appropriately fastening to the substrate and then observing for panel flatness or signs of oil canning.
By following the procedure as described above, the moment at which oil canning is first observed should be noted. If you notice what you perceive as excessive oil canning at any point, stop the installation and have the owner of the project review it to determine further steps.
7 Ways to Minimize Oil Canning on Metal Roofing
Luckily, there are specific methods and practices that will help minimize the chance of oil canning development. Before we begin, please keep in mind that doing one or more of these recommendations does not mean you won’t have oil canning; sometimes it’s just an inherent and unavoidable variable with metal.
#1: Purchase a thicker metal material
One of the easier solutions to minimize oil canning is to purchase a thicker metal because it’s harder for the metal to give in and move.
#2: Use a rib roller to break up the flat space on a panel
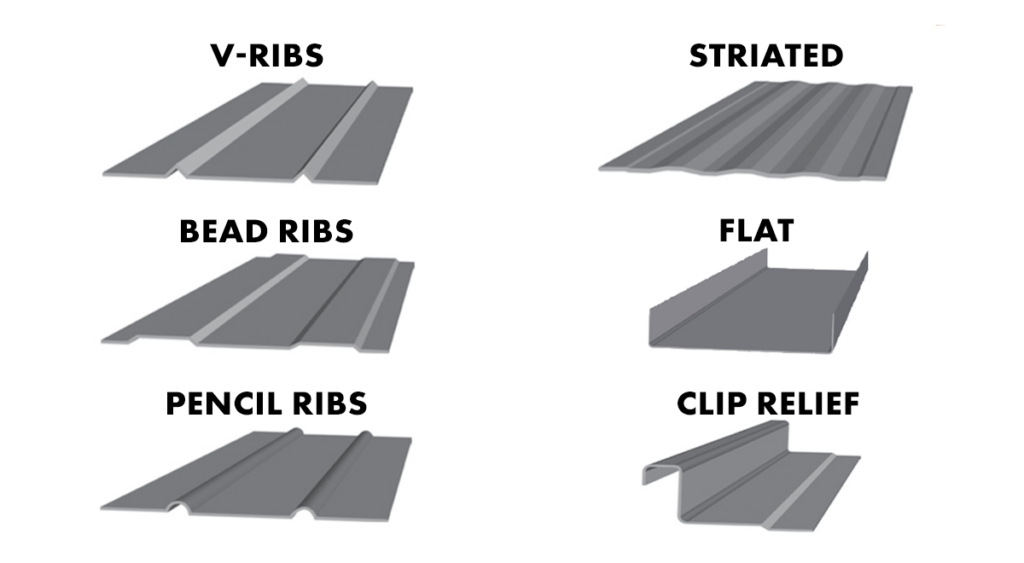
Rib rollers (also called stiffening ribs or striations) are the manufactured indentations or “patterns” rollformed into the flat portion of metal panels between the seams. While these indentations don’t prevent oil canning from happening, it does break up the amount of flat surface and makes the waviness less apparent. Common rib rollers include:
- Ribbed
- V-Ribs
- Bead
- Pencil
- Striated
- Corrugated
- Clip relief
#3: Install the metal panels on a leveled, consistent, and in-plane roof deck
An uneven roof deck, whether it’s made of metal, plywood, or oriented strand board (OSB), is one of the most common reasons oil canning occurs. If the metal panels are installed on top of one that bows or is inconsistent in its plane, stresses are inflicted on the metal as it tries to conform to this uneven surface. Always use the proper methods to ensure the roof deck is level before any panels or accessories/components are installed.
#4: Use a low-gloss or matte finish to reduce reflectivity
Because the amount of light reflecting off of a metal roof or wall system makes such a difference in regards to the visibility of oil canning, using a coil or sheet with a low-gloss or matte finish is the best way to ensure reflectivity is reduced.
#5: Install panels with narrow widths
Since oil canning tends to be most visible in the broad, flat areas of a metal roof or wall system, reducing the amount of those flat areas by choosing smaller and narrower panel widths (18” or less) is a common practice.
#6: Buy tension-leveled metal
Tension-leveled, or stretched, metal is a coil that has already been stretched beyond its yield point where it can no longer return to its original state. This means the metal won’t warp or create waviness, making it a great buying choice.
#7: Use backer rod or other similar shimming material
The addition of backer rods or shimming materials under the clips to help flatten out uneven roof planes can help relieve oil canning in some cases. According to the MCA’s technical bulletin on oil canning:
“Some designers specify the use of ‘backer rod’ or other similar types of shimming materials on the panel underside when installation is over a solid substrate. Backer rod is a compressible foam strip normally used in the concrete and masonry trades in joints to serve as a backing for a caulk joint. For certain types of metal panel systems, it causes the center of the panel to ‘pillow’ uniformly, relieving stress and reducing the visual effects of oil canning.”
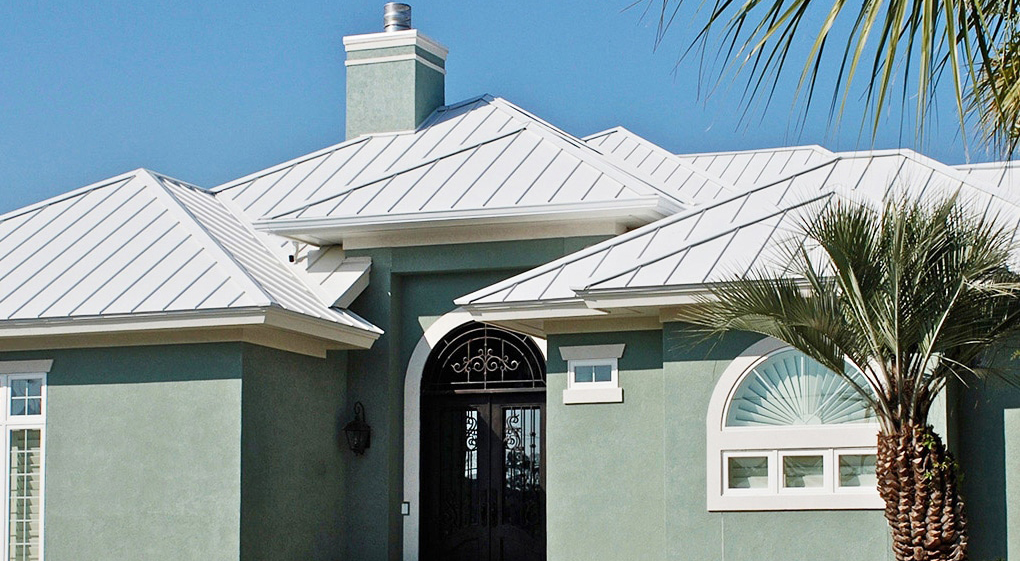
Final Thoughts on Oil Canning
Here is our recommendation: Be as realistic and understanding as possible with your expectations when it comes to oil canning.
Unfortunately, there is no 100% cure or remedy that will protect against oil canning, especially because it’s just the nature of metal to try to revert back to its original form. The best thing you can do is to stay alert and recognize oil canning before it’s installed so no cost/labor tear up is needed after installation. If you follow the recommendations discussed in this article, you’ll have a better chance of reducing or even eliminating this problem before it starts.
That being said, if you do notice some mild oil canning, many metal roofs and wall systems will work out some of the stresses as time passes, so it might take several seasons for the metal to settle and adapt.
Here at Sheffield Metals, we’re dedicated to providing you with honest answers about oil canning so you get the best end product possible. Contact us today to speak with one of our experienced metal roof professionals.
